Crompton graves 107/54 65mm Copper winding data
S.NO. | TERMS | VALUES |
1. | STAMPING TYPE | HR/CRNO |
2. | O/D – I/D | 107/54MM |
3. | LENGTH | 65MM |
4. | SLOT | 24 |
5. | SWG-R | 26×26 |
6. | PITCH-R | 1-6,1-8,1-10,1-12 |
7. | TURNS-R | 45, 45, 45, 45 |
8. | SWG-S | 26 |
9. | PITCH-S | 1-10,1-12 |
10. | TURNS-S | 90, 90 |
11. | WEIGHT-R | 450g |
12. | WEIGHT-S | 250g |
13. | RPM | 2880 |
14. | CAPACITOR | 18-20 MFD |
15. | WINDING WIRE | COPPER |
16. | CONNECTION TYPE | SERIES |
### Copper Winding Data for Crompton Graves 107/54 65mm Motors
The following table provides detailed specifications for the copper winding data of Crompton Graves 107/54 65mm motors:
| S.NO. | TERMS | VALUES |
|——-|——————–|—————-|
| 1. | STAMPING TYPE | HR/CRNO |
| 2. | O/D – I/D | 107/54MM |
| 3. | LENGTH | 65MM |
| 4. | SLOT | 24 |
| 5. | SWG-R | 26×26 |
| 6. | PITCH-R | 1-6, 1-8, 1-10, 1-12 |
| 7. | TURNS-R | 45, 45, 45, 45 |
| 8. | SWG-S | 26 |
| 9. | PITCH-S | 1-10, 1-12 |
| 10. | TURNS-S | 90, 90 |
| 11. | WEIGHT-R | 450g |
| 12. | WEIGHT-S | 250g |
| 13. | RPM | 2880 |
| 14. | CAPACITOR | 18-20 MFD |
| 15. | WINDING WIRE | COPPER |
| 16. | CONNECTION TYPE | SERIES |
### Explanation of Terms
#### Stamping Type
– **HR/CRNO**: Hot Rolled / Cold Rolled Non-Oriented steel, used for the motor’s core laminations to reduce eddy current losses and improve efficiency.
Outer Diameter (O/D) – Inner Diameter (I/D)
– **107/54MM**: The outer diameter is 107mm, and the inner diameter is 54mm, indicating the core size.
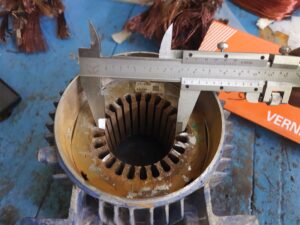
Length
– **65MM**: The length of the core or the stack height.
Slot
– **24**: Number of slots in the stator for winding.
SWG-R (Standard Wire Gauge – Rotor)
– **26×26**: Indicates the gauge of the wire used for rotor windings.
Pitch-R (Rotor Winding Pitch)
– **1-6, 1-8, 1-10, 1-12**: Different winding pitches used for the rotor.
#### Turns-R
– **45, 45, 45, 45**: Number of turns for each of the rotor windings.
#### SWG-S (Standard Wire Gauge – Stator)
– **26**: Indicates the gauge of the wire used for stator windings.
#### Pitch-S (Stator Winding Pitch)
– **1-10, 1-12**: Different winding pitches used for the stator.
#### Turns-S
– **90, 90**: Number of turns for each of the stator windings.
#### Weight-R and Weight-S
– **450g** (Rotor) and **250g** (Stator): Weight of the copper wire used for rotor and stator windings, respectively.
#### RPM
– **2880**: Rotations per minute, indicating the motor speed.
#### Capacitor
– **18-20 MFD**: Microfarad rating of the capacitor used in the motor.
#### Winding Wire
– **COPPER**: Indicates that copper wire is used for the windings, which offers better conductivity and efficiency.
#### Connection Type
– **SERIES**: The type of electrical connection used for the windings.
Motor Winding Techniques and Best Practices
1. **Consistent Tension**: Maintain consistent tension during winding to ensure uniform coils and avoid damage to the wire. Inconsistent tension can lead to performance issues and mechanical imbalances.
2. **Proper Layering**: Ensure proper layering of the wire without overlaps to prevent short circuits and enhance cooling. Proper layering also improves the motor’s efficiency by reducing resistance.
3. **Quality Materials**: Use high-quality enamel-coated copper wire to reduce resistance and improve efficiency. The enamel coating provides necessary insulation, and high-purity copper ensures optimal conductivity.
4. **Slot Fill Factor**: Maximize the slot fill factor, which is the ratio of copper to the total slot area. A higher slot fill factor reduces electrical resistance and improves the motor’s performance.
5. **Cooling Mechanisms**: Incorporate effective cooling mechanisms, such as fans or heat sinks, to manage heat dissipation. Proper ventilation and thermal management are crucial for maintaining optimal operating temperatures and extending the motor’s lifespan.
6. **Balancing**: Ensure the rotor and stator are properly balanced to minimize vibration and noise. Dynamic balancing techniques can help achieve precise balance, enhancing the motor’s overall stability and performance.
7. **Testing**: Conduct rigorous testing, including resistance, inductance, and insulation resistance tests, to verify the quality of the winding. Thermal imaging can be used to detect hotspots and ensure even heat distribution.
By following these guidelines and maintaining attention to detail, you can ensure that the Crompton Graves 107/54 65mm motor operates efficiently and reliably, meeting the performance expectations and providing long-term service.